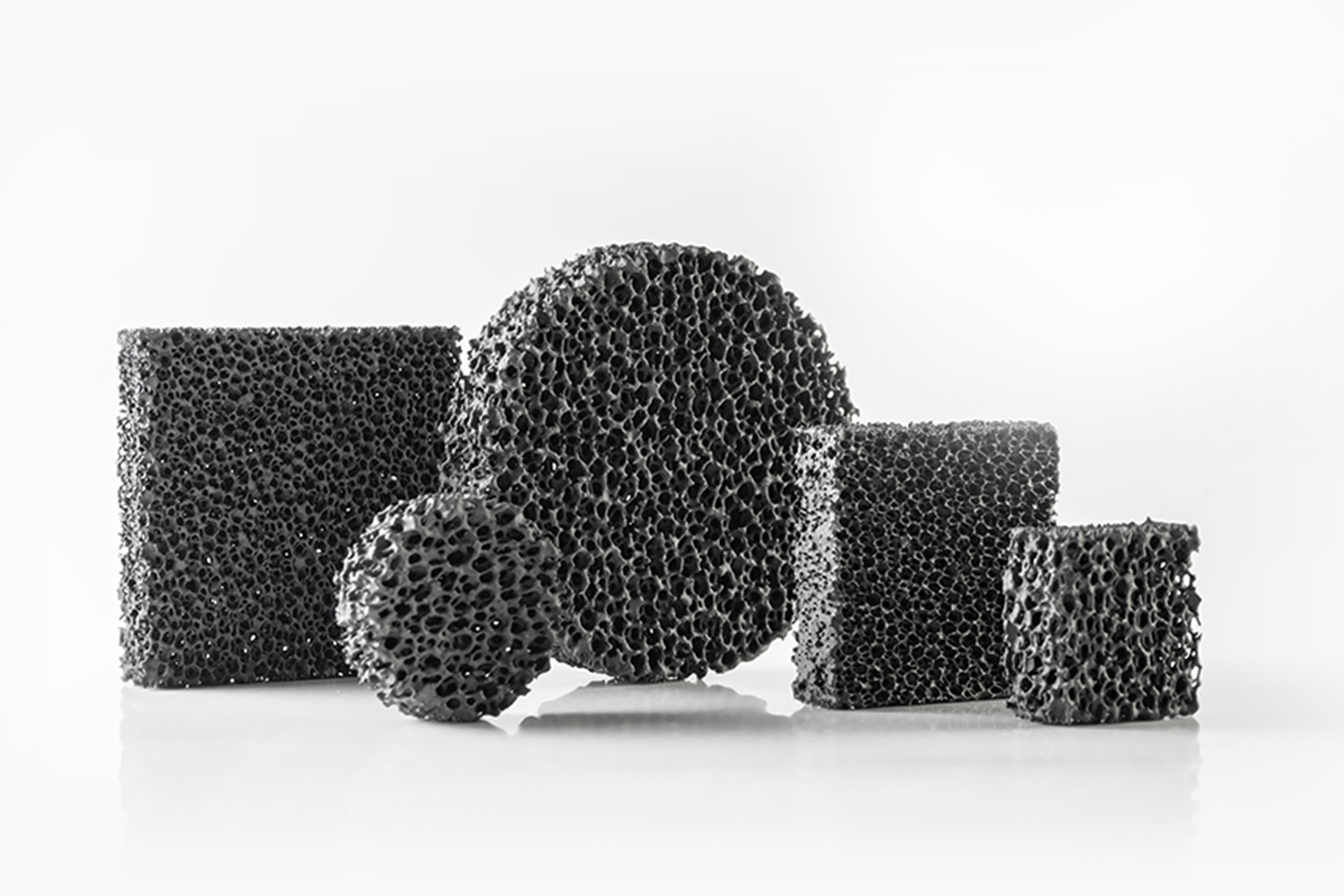
Product details
The Al2O3 – C based filters are intended for filtering ferrous metals up to the temperatures of 1700 °C.
VUKOPOR® HTX ceramic foam filters are designed for filtering of steel and heavy iron castings up to the temperature of 1700 °C.
The structure of VUKOPOR® HTX filter is created by a three – dimensional network of open pores, forming a labyrinth of the filter body. These filter properties ensure optimum conditions for utilization of all mechanisms of efficient filtration. Like other types of foam ceramic filters, they help to remove undesirable impurities from filtered metal and provide regular filling of mould cavities without any turbulence of the melt. Thanks to this feature the erosion of sand moulds and reoxidation of the melt behind the filter is minimized.
VUKOPOR® HTX filters can be placed directly into the “filter prints” of the gating systems or may be used for “direct casting on filter”, usually in combination with exothermic sleeves. They are successfully applied where a zircon oxide-based ceramic filters may not be used because of their high thermal capacity causing the filter “freeze-off”.
VUKOPOR® HTX filters may not be used for low – carbon alloys with carbon content less than 0.16 p.c. where they become a secondary source of carbon. The filters may not be used in Investment Casting process as well, where is needed to anneal filters inside ceramic shells before pouring.
High filter stability during casting, outstanding thermal conductivity and low weight create the preconditions for fast filter heating/priming and minimize temperature losses. By their features they are predetermined for direct casting through the exothermic sleeves and for filtering larger nodular iron castings.